ビジネスQ&A
工場改善・効率化のための5Sの取り組み方法を教えてください。
効率化につながる工場管理・改善の実践方法の基礎として5Sの取り組みがあると思いますが、5Sは本当に効率化につながるのでしょうか?現場には標語をかかげて内容も説明していますが、少しも効果が分かりません。やり方が悪いのでしょうか?どのようにやれば、効率化につながるのでしょうか。
回答
工場管理・改善の基礎として5Sがあります。5Sの意義をもう一度明確にし、社長さん自らの行動などで、社内の意思統一と理解を図って、全社的に推進する体制を整備しましょう。そして、徹底的な整理に取り組み、知恵と試行錯誤で整頓を進めましょう。
5Sとは「整理・整頓・清掃・清潔・躾」の略であり、その定着は、効率化につながる工場管理・改善の基礎です。まず、5Sの中身をもう一度振り返りましょう。
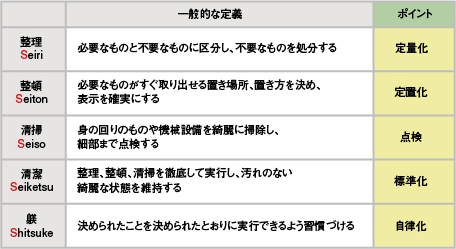
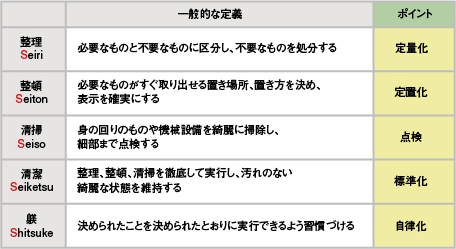
【工場の課題解決の基礎】
工場では、ものを探すということがあたり前になっていませんか。部品を探す。工具を探す。指示書を探す。探すことが多くて時間がかかるほど、当然生産性は低下します。
また、工場内はさまざまな作業や加工を通して、ゴミや汚れがたくさん発生します。機械操作や製品の取扱いには、危険を伴うこともあるでしょう。ゴミや汚れが製品についていたら、それは不良品となってしまうでしょう。また、ゴミや汚れが原因で機械が故障することもあるでしょう。危険を軽視すると、ちょっとしたケガで作業が遅れるようなことが起きるばかりではなく、工場全体に及ぶ大きな事故につながる可能性もあるでしょう。
このようなことに対して、いらない機械や材料を整理(廃棄)すれば、作業スペースが広がって作業がやりやすくなるだけでなく、必要なものも探しやすくなるでしょう。そのうえ、道具などをどこに置くかを決めるだけでも、探す効率は格段によくなるでしょう。置き方、戻し方を工夫すれば、さらに効果アップが期待できます。
作業場や機械を清掃して、常に清潔を保てば、職場環境の改善によって、作業意欲が増すことが期待できるばかりでなく、機械の性能維持にも効果があると言えるでしょう。
このように、工場の課題を解決していくための基礎として、5Sがあります。5Sの実施は、生産性の改善、作業環境の改善などに直接的にまた間接的にさまざまな効果をもたらし、工場全体の改善につながっていくのです。
しかし、簡単そうでいて難しいのも事実です。標語や口頭での説明だけでスムーズに行われるものではありません。工場長さんはもちろん、社長さん自らが実行の推進役になり、全社をあげて取り組む必要があります。
それでは、具体的にはどのような点に留意して5Sを進めればよいのでしょうか。
【整理と整頓】
5Sの要は整理と整頓です。そして、生産性の向上につながる整頓をするためには、徹底的に整理に取り組むことが重要です。整理ができて、初めて整頓があります。整理ができなければ、5Sは成り立ちません。ですから、この整理にこそ、社長さんの決意と行動が必要なのです。もちろん、躾も社長さんの役割のようではありますが、自らが行動しない躾は浸透しにくいものです。躾の重要性を理解し、効果的な躾を行いたいならば、整理という行動の中で、社長さんの決意と姿勢を示しましょう。
また、整頓では作業効率改善につながる具体的な仕組みがつくられますが、これはいわばアイデアです。改善や効率アップのノウハウではありますが、原動力ではありません。改善や効率アップの基礎として5Sがあり、その基盤が整理です。このように考えれば、整理の具体的な方法論である、「赤札作戦」も徹底的で思い切ったもの=正しい「赤札作戦」になるのではないでしょうか。
赤札作戦とは、工場にあるものを、「要るもの」と「要らないもの」に分ける方法ですが、ここで、念のため、「赤札作戦」の進め方の概略について、確認しておきましょう。
まず、「品名」や「数量」、「停滞期間」などを記入できるA4程度の大きさの赤い札(赤札)を用意します。この赤札を工場にある在庫品や設備などに貼るわけですが、あらかじめ、貼る基準を設定しておきます。たとえば、これから1カ月の生産計画の中で、使うものは「要るもの」、使わないものは「赤札」を貼るというルールを設定したり、使う予定が分からないものは、赤札を貼っておく期間(例:材料は1カ月、機械は3カ月、スペースは1カ月など)を決めて、その期間内に使ったら赤札を剥がし、赤札を剥がしたものは「要るもの」、赤札が貼ってあるままのものは「要らないもの」とするなどです。
そして、部品や材料、仕掛品、製品などの在庫品や、機械や机などの設備、床や棚などのスペースに、実際に赤札を貼ります。その後、ルールにしたがい赤札が貼られているかいないかで、「要るもの」と「要らないもの」を判断します。
この「赤札作戦」によって、「要るもの」と「要らないもの」をわけたら、「要らないもの」の整理を実行するわけです。
次は整頓です。整頓は、先ほど触れましたとおり、作業効率改善、効率アップにつながるノウハウの塊のようなものです。いかに知恵を出すか、そして、常に試行錯誤をしてより高いレベルを目指す気持ちを持ち続けられるかが、たいへんな重要な要素です。そして、この整頓の差こそが、作業効率や利益を生み出す仕組みの差につながってきます。「看板作戦」や物の形跡管理、「一発確認(ひと目みただけで、状態の確認ができたり、警告音などで、見る動作をしなくても次の行動につながるような仕組み)」など、すでにほかの工場で活用されている方法を取り入れることも大切です。そしてさらに、自社の工場にあった、あるいは自社の生産形態に合った工夫を、現場主導で考える環境づくりに取り組んでみましょう。
【清掃と清潔】
清掃には、整理、整頓を点検する役割があります。常に「きれい」を保つことが清掃ですが、同時に、清掃によって作業現場や設備、作業状態を管理、点検するという目的も意識しましょう。整理と整頓までできている工場では、余計な作業と思われかねません。が、点検であるという位置付けであれば、価値が違ってくるでしょう。また、「きれい」を保つための単なる作業としての清掃を不要にするのが、清潔ということです。汚れてから掃除をするのではなく、汚れない仕組みが大切だということです。清掃、清潔で整理、整頓を維持管理しましょう。
【躾とは】
そしてこれら、整理、整頓、清掃、清潔の4Sをいつも正しく守り、確実に実行する習慣付けが躾です。これらの4Sを推進し、発展させる役割が躾なのです。5Sの要は整理と整頓ですが、5Sを実行する際にもっとも重要なのが、この躾ということなのです。そして躾の第一歩は挨拶であり、挨拶はコミュニケーションの入口です。
良好なコミュニケーションは、会社の共通目的に向けての個人の貢献意欲を引き出すことにつながります。個人の貢献意欲が5Sの定着につながり、継続的な工場改善の基礎となります。
社長さんのやる気、リーダーや現場の作業員一人ひとりのやる気こそが5S成功の鍵です。5Sを定着させるために、社長さん自らの行動や、社内セミナーなど、社内の意思統一と理解を図って、全社的に推進する体制とやる気を整備しましょう。
- 回答者
-
中小企業診断士 小林 弘幸
同じテーマの記事
- 工場を新設したいのですが、影響を受ける法規制について教えてください。
- 設備投資計画における採算性の計算方法について教えてください。
- 工場改善・効率化のための5Sの取り組み方法を教えてください。
- 私の工場内の「ムダ取り」をしたいのですが、どのようにすればよいのですか?
- 古い工場なので地震が心配です。どのような対策をとればよいですか?
- 現場での5S運動定着化のための考え方、行動の仕方は?
- 自社の技術的課題を解決したいのですが、何かよい支援制度がありましたら教えてください。
- 研究開発補助金の申請をしたいのですが、どのような点に気を付けて申請すればよいのでしょうか?
- ムダのない段取り改善の方法について教えてください。
- 不良品を出さないための工程管理方法について教えてください。
- 老朽化した設備の管理方法について教えてください。
- 経験の浅いパート社員の作業を指導する方法を教えてください。
- 製品開発に環境・リサイクル面で配慮すべきポイントを教えてください。
- 「見える化」とはどういうことなのでしょうか?
- 製造業での検査の基本となる官能検査について教えてください。
- 新製品のアイデアを考える良い方法があれば教えてください。
- 5S活動を実施していますが、うまく活動が進みません。効果的な実施方法を教えてください。
- 作業標準書の必要性とその内容について教えてください。
- HACCPとはどのような品質管理手法なのか教えてください。
- 生産設備の地震対策はどうすればよいでしょうか。
- 多品種少量生産における効率的な生産方法を教えてください。
- NC工作機械導入のメリット・デメリットを教えてください。
- 製造現場での「ムダ」取りについて教えてください。
- リーン生産方式と従来の生産方式の違いについて教えてください。